Definition and Methods of Curing of Concrete
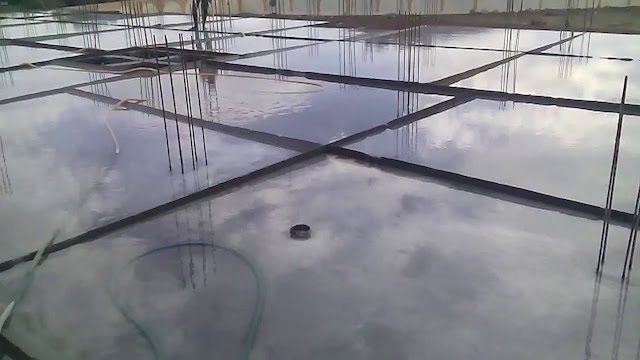
See Also: Maturity of Concrete
Definition:
Curing can be described as keeping the concrete moist and warm enough so that the hydration of cement can continue. More elaborately, it can be described as the process of maintaining a satisfactory moisture content and a favorable temperature in concrete during the period immediately following placement, so that hydration of cement may continue until the desired properties are developed to a sufficient degree to meet the requirement of service. If curing is neglected in the early period of hydration, the quality of concrete will experience a sort of irreparable loss. An efficient curing in the early period of hydration can be compared to a good and wholesome feeding given to a new born baby.
Methods of Curing of Concrete
Concrete curing methods may be divided broadly into four categories:
- Water curing
- Membrane curing
- Application of heat
- Miscellaneous
Water Curing
This is by far the best method of curing as it satisfies all the requirements of curing, namely, promotion of hydration, elimination of shrinkage and absorption of the heat of hydration. It is pointed out that even if the membrane method is adopted, it is desirable that a certain extent of water curing is done before the concrete is covered with membranes. Water curing can be done in the following ways:
a. Immersion
Keep concrete in water
Keep the concrete immersed in water during the curing period to fulfill the moisture requirements of concrete. This can be done by:
- Ponding or immersion
- Spraying or fogging
- Fogging minimizes moisture loss during and after placing and finishing of concrete.
- Saturated wet coverings
Such methods provide some cooling through evaporation, which is beneficial in hot weather.
b. Ponding
c. Spraying or Fogging
d. Wet Covering
Prevent the loss of the existing water
Prevent the loss of the mixing water from concrete by sealing its surface. This can be done by:
- Covering the concrete with impervious paper or plastic sheets.
- Polyethylene film is an effective moisture barrier for curing concrete and easily applied to complex as well as simple shapes. To minimize discoloration, the film should be kept as flat as possible on the concrete surface.
- Applying membrane-forming curing compounds.
- Penetrating sealers help protect reinforcing steel in bridge decks from corrosion due to chloride infiltration without reducing surface friction
The precast concrete items are normally immersed in curing tanks for a certain duration. Pavement slabs, roof slab etc. are covered under water by making small ponds. Vertical retaining wall or plastered surfaces or concrete columns etc. are cured by spraying water. In some cases, wet coverings such as wet gunny bags, hessian cloth, jute matting, straw etc., are wrapped to vertical surface for keeping the concrete wet. For horizontal surfaces saw dust, earth or sand are used as wet covering to keep the concrete in wet condition for a longer time so that the concrete is not unduly dried to prevent hydration.
Membrane Curing
Sometimes, concrete works are carried out in places where there is acute shortage of water. The lavish application of water for water curing is not possible for reasons of economy. Curing does not mean only application of water; it means also creation of conditions for promotion of uninterrupted and progressive hydration. It is also pointed out that the quantity of water, normally mixed for making concrete is more than sufficient to hydrate the cement, provided this water is not allowed to go out from the body of concrete. For this reason, concrete could be covered with membrane which will effectively seal off the evaporation of water from concrete. Large numbers of sealing compounds have been developed in recent years. The idea is to obtain a continuous seal over the concrete surface by means of a firm impervious film to prevent moisture in concrete from escaping by evaporation. Some of the materials, which can be used for this purpose, are bituminous compounds, polyethylene or polyester film, waterproof paper, rubber compounds etc. When waterproofing paper or polyethylene film are used as membrane, care must be taken to see that these are not punctured anywhere and also see whether adequate lapping is given at the junction and this lap is effectively sealed.
Application of heat
The development of strength of concrete is a function of not only time but also that of temperature. When concrete is subjected to higher temperature it accelerates the hydration process resulting in faster development of strength. Concrete cannot be subjected to dry heat to accelerate the hydration process as the presence of moisture is also an essential requisite. Therefore, subjecting the concrete to higher temperature and maintaining the required wetness can be achieved by subjecting the concrete to steam curing. A faster attainment of strength will contribute to many other advantages mentioned below. The exposure of concrete to higher temperature is done in the following manner:
a. Steam curing at ordinary pressure
Steam Curing
Strength gain can also be accelerated with:
- Live steam
- Heating coils
- Electrically heated forms or pads
b. Steam curing at high pressure
c. Curing by Infra-red radiation
d. Electrical curing.
Miscellaneous Methods of Curing
Calcium chloride is used either as a surface coating or as an admixture. It has been used satisfactorily as a curing medium. Both these methods are based on the fact that calcium chloride being a salt shows affinity for moisture. The salt not only absorbs moisture from atmosphere but also retains it at the surface. This moisture held at the surface prevents the mixing water from evaporation and thereby keeps the concrete wet for a long time to promote hydration. Formwork prevents escaping of moisture from the concrete, particularly, in the case of beams and columns. Keeping the form work intact and sealing the joint with wax or any other sealing compound prevents the evaporation of moisture from the concrete. This procedure of promoting hydration can be considered as one of the miscellaneous methods of curing.
Curing Time
- Time - 3-7 Days
- Temperature - 50-100 F
- Moisture - Saturated at all times