Headrace Pressure Flow in Steel Pipes
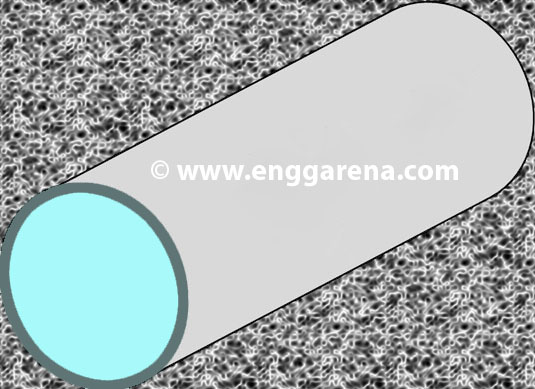
Headrace pipe can also serve the same function as that of Headrace tunnels, depending upon the site location, geological and topographical constraints. as discussed earlier that tunnels can be divided into two types on the basis of type of flow
- Pressure Flow Tunnels
- Gravity Flow Tunnels.
Similarly headrace pipes can also be divided into two categories pressure flow and gravity flow. Following are the design examples of the two types:
Hydraulic Design of Pressure Flow in Headrace Pipes (STEEL)
Let suppose a 50 cumecs needs to be passed through 4.0m diameter steel pipe with a total length of 1000m, longitudinal slope of 1/1000 m, Mannng’s coefficient of 0.014 (steel) and with a gross head of 100m.
Hydraulic Design Calculations of Headrace Pipe (Pressure Flow)
BASIC DATA |
|
|
|
|
Pipe invert elevation at Start |
I.L.1 |
= |
100.00 |
m a.s.l. |
Design discharge |
Q |
= |
50.0 |
m3/s |
Internal diameter of pipe |
D |
= |
4.00 |
m |
Flow velocity |
V |
= |
4.0 |
m/s |
Hydraulic radius |
R |
= |
1.00 |
m |
Maximum Gross Head |
H |
= |
100.00 |
m |
Effective head from center of pipe |
he |
= |
10.0 |
m |
Max. possible flow velocity (orifice flow) |
VOmax |
= |
8.40 |
m/s |
Max. possible discharge (orifice flow) |
QOmax |
= |
105.61 |
m3/s |
Alternatively Using another equation |
|
|
|
|
Max. possible discharge (conduit flow) |
QCmax |
= |
147.1 |
m3/s |
Check QOmax ≥ Q |
|
= |
O.K. |
|
Total length of pipe (Δx) |
L |
= |
1000.0 |
m |
Longitudinal slope |
S |
= |
0.0010 |
m/m |
Hazen-Williams roughness coefficient |
C |
= |
120 |
|
Mannings friction factor (steel) |
n |
= |
0.0140 |
|
Friction factor (Moody) |
f |
= |
0.0130 |
|
FRICTION FACTOR |
|
|
|
|
Using Reynolds number |
|
|
|
|
Kinematic viscosity of water at 20oC |
ν |
= |
1.0E-06 |
m2/s |
Reynolds number |
Re |
= |
15915494 |
|
Check Re ≤ 2000 |
|
= |
TURBULENT |
|
Roughness height (welded steel) |
e |
= |
0.600 |
mm |
Ratio |
e/D |
= |
0.00015 |
|
|
1 |
= |
1.00 |
|
Friction factor (Moody) |
f |
= |
0.01304 |
|
SUBMERGENCE REQUIREMENTS |
|
|
|
|
Minimum submergence (by Knauss) |
Smin |
= |
9.84 |
m |
" " " " (by Rohan) |
Smin |
= |
8.20 |
m |
" " " " (by Gordon) |
Smin |
= |
5.77 |
m |
Minimum submergence |
Smin |
= |
7.94 |
m |
Provided submergence |
SPr |
= |
10.00 |
m |
Check SPr ≥ Smin |
|
= |
O.K. |
|
HEADLOSSES |
|
|
|
|
FRICTION LOSS |
|
|
|
|
Headloss (Manning) |
hf |
= |
3.10 |
m |
Headloss (Hazen-Williams) |
hf |
= |
2.46 |
m |
Headloss (Darcy-Weisbach) |
hf |
= |
2.63 |
m |
Using Colebrook - White equation |
1 |
= |
1.00 |
|
Friction loss (Colebrook-White) |
hf |
= |
2.63 |
m |
Maximum friction headloss |
hfmax |
= |
3.10 |
m |
BEND LOSS |
|
|
|
|
No. of bends |
nB |
= |
10 |
no. |
Headloss in bends |
hLB |
= |
1.21 |
m |
ENTRANCE LOSS |
|
|
|
|
Velocity at pipe bellmouth |
vE |
= |
0.46 |
m/s |
Entrance headloss |
hLE |
= |
0.0011 |
m |
Total headloss in headrace pipe |
hLT |
= |
4.31 |
m |
WALL THICKNESS |
|
|
|
|
Bulk modulus of water |
k |
= |
2.1E+09 |
N/m2 |
Modulus of elasticity of pipe material |
E |
= |
2.1E+11 |
N/m2 |
Wall thickness (provided) |
ts |
= |
25.0 |
mm |
Hydrostatic pressure |
Pw |
= |
10.00 |
kN/mm2 |
Weld efficiency |
kf |
= |
0.95 |
|
Allowable tensile stress |
σf |
= |
1400 |
kN/mm2 |
Corrosion allowance |
cs |
= |
1.5 |
mm |
Wall thickness (required) |
ts |
= |
15.04 |
mm |
Wall thickness (provided) |
ts |
= |
25.0 |
mm |
Density of steel |
ρs |
= |
7850.0 |
kg/m3 |
Minimum thickness of steel sheet |
tmin |
= |
11.25 |
mm |
Effective thickness of pipe |
te |
= |
23.50 |
mm |
Check te ≥ tmin |
|
= |
O.K. |
|
Hoop stress |
σH |
= |
851.06 |
kgf/cm2 |
Check σH ≤ 1.5yield stress |
|
= |
O.K. |
|
STEEL QUANTITY |
|
|
|
|
X-sectional area of steel |
As |
= |
0.316 |
m2 |
Volume of steel |
Vs |
= |
316.12 |
m3 |
Weight of steel |
Ws |
= |
2481.56 |
tons |
Weight of steel (5% increse for joints) |
Ws |
= |
2605.64 |
tons |
Width of steel sheet |
w |
= |
12.72 |
m |
Length of steel sheet |
l |
= |
6.0 |
m |
No. of steel sheets |
n |
= |
167 |
no. |
BASIC DATA |
|
|
|
|
Pipe invert elevation at Start |
I.L.1 |
= |
100.00 |
m a.s.l. |
Design discharge |
Q |
= |
50.0 |
m3/s |
Internal diameter of pipe |
D |
= |
4.00 |
m |
Flow velocity |
V |
= |
4.0 |
m/s |
Hydraulic radius |
R |
= |
1.00 |
m |
Maximum Gross Head |
H |
= |
100.00 |
m |
Effective head from center of pipe |
he |
= |
10.0 |
m |
Max. possible flow velocity (orifice flow) |
VOmax |
= |
8.40 |
m/s |
Max. possible discharge (orifice flow) |
QOmax |
= |
105.61 |
m3/s |
Alternatively Using another equation |
|
|
|
|
Max. possible discharge (conduit flow) |
QCmax |
= |
147.1 |
m3/s |
Check QOmax ≥ Q |
|
= |
O.K. |
|
Total length of pipe (Δx) |
L |
= |
1000.0 |
m |
Longitudinal slope |
S |
= |
0.0010 |
m/m |
Hazen-Williams roughness coefficient |
C |
= |
120 |
|
Mannings friction factor (steel) |
n |
= |
0.0140 |
|
Friction factor (Moody) |
f |
= |
0.0130 |
|
FRICTION FACTOR |
|
|
|
|
Using Reynolds number |
|
|
|
|
Kinematic viscosity of water at 20oC |
ν |
= |
1.0E-06 |
m2/s |
Reynolds number |
Re |
= |
15915494 |
|
Check Re ≤ 2000 |
|
= |
TURBULENT |
|
Roughness height (welded steel) |
e |
= |
0.600 |
mm |
Ratio |
e/D |
= |
0.00015 |
|
|
1 |
= |
1.00 |
|
Friction factor (Moody) |
f |
= |
0.01304 |
|
SUBMERGENCE REQUIREMENTS |
|
|
|
|
Minimum submergence (by Knauss) |
Smin |
= |
9.84 |
m |
" " " " (by Rohan) |
Smin |
= |
8.20 |
m |
" " " " (by Gordon) |
Smin |
= |
5.77 |
m |
Minimum submergence |
Smin |
= |
7.94 |
m |
Provided submergence |
SPr |
= |
10.00 |
m |
Check SPr ≥ Smin |
|
= |
O.K. |
|
HEADLOSSES |
|
|
|
|
FRICTION LOSS |
|
|
|
|
Headloss (Manning) |
hf |
= |
3.10 |
m |
Headloss (Hazen-Williams) |
hf |
= |
2.46 |
m |
Headloss (Darcy-Weisbach) |
hf |
= |
2.63 |
m |
Using Colebrook - White equation |
1 |
= |
1.00 |
|
Friction loss (Colebrook-White) |
hf |
= |
2.63 |
m |
Maximum friction headloss |
hfmax |
= |
3.10 |
m |
BEND LOSS |
|
|
|
|
No. of bends |
nB |
= |
10 |
no. |
Headloss in bends |
hLB |
= |
1.21 |
m |
ENTRANCE LOSS |
|
|
|
|
Velocity at pipe bellmouth |
vE |
= |
0.46 |
m/s |
Entrance headloss |
hLE |
= |
0.0011 |
m |
Total headloss in headrace pipe |
hLT |
= |
4.31 |
m |
WALL THICKNESS |
|
|
|
|
Bulk modulus of water |
k |
= |
2.1E+09 |
N/m2 |
Modulus of elasticity of pipe material |
E |
= |
2.1E+11 |
N/m2 |
Wall thickness (provided) |
ts |
= |
25.0 |
mm |
Hydrostatic pressure |
Pw |
= |
10.00 |
kN/mm2 |
Weld efficiency |
kf |
= |
0.95 |
|
Allowable tensile stress |
σf |
= |
1400 |
kN/mm2 |
Corrosion allowance |
cs |
= |
1.5 |
mm |
Wall thickness (required) |
ts |
= |
15.04 |
mm |
Wall thickness (provided) |
ts |
= |
25.0 |
mm |
Density of steel |
ρs |
= |
7850.0 |
kg/m3 |
Minimum thickness of steel sheet |
tmin |
= |
11.25 |
mm |
Effective thickness of pipe |
te |
= |
23.50 |
mm |
Check te ≥ tmin |
|
= |
O.K. |
|
Hoop stress |
σH |
= |
851.06 |
kgf/cm2 |
Check σH ≤ 1.5yield stress |
|
= |
O.K. |
|
STEEL QUANTITY |
|
|
|
|
X-sectional area of steel |
As |
= |
0.316 |
m2 |
Volume of steel |
Vs |
= |
316.12 |
m3 |
Weight of steel |
Ws |
= |
2481.56 |
tons |
Weight of steel (5% increse for joints) |
Ws |
= |
2605.64 |
tons |
Width of steel sheet |
w |
= |
12.72 |
m |
Length of steel sheet |
l |
= |
6.0 |
m |
No. of steel sheets |
n |
= |
167 |
no. |