Types of Metals used in Civil Engineering
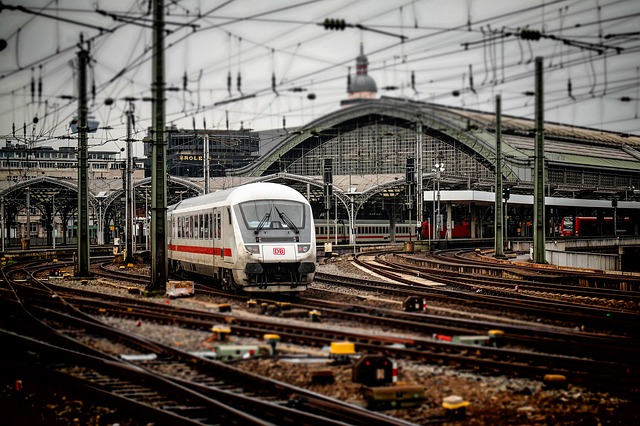
All metals used for engineering works are classified into:
- Ferrous metals
- Non-Ferrous metals: Wherein iron is not the main constituent (Copper, Aluminum, Zinc and lead etc)
Ferrous metals:
Wherein iron is the main constituent (Cast iron, wrought iron and different forms of steels)
Ferrous metals ► not directly obtained from iron ores
PIG IRON:
From iron ore ► impure form of metal ► Pig iron
It is the pig iron which further yields “Ferrous metals”
Pig iron is not suitable for any mechanical use unless it is converted into cast iron, wrought iron or steel
Cast Iron:
When Pig Iron is re melted with limestone and coke and poured into moulds of desired shapes and sizes a purer product results known as cast iron. Carbon content in cast iron varies from 2 to 5%. During re melting of pig iron, scrap iron may also be added for economy.
Properties of Cast Iron
- It is brittle, non ductile, non malleable and cracks when subjected to shocks
- It cannot be magnetized
- It does not rust
- It is strong in compression but weak in tension and shear
- Its melting point is 12000C
- Its specific gravity is 7.5
USES
Weak in tension therefore cannot be used in construction
Can be used for parts of pumps, motors, engines etc
Because of corrosion resistance ►can be used for pipes to some extent
WROUGHT IRON
When pig iron is melted in such a way as to remove all of the carbon and other impurities, the result is wrought iron
Good quality wrought iron contains 99.5 % iron, less than 0.1 % of Silicon, 0.01 % of Sulfur, 0.07 % of phosphorus and 0.03 % of manganese.
Properties of Wrought Iron
- Wrought iron is very malleable and ductile
- Its tensile strength is 20-26 tons /in2
- It is strong in compression but not so strong as steel
- It can be easily worked, welded and is tough
- Its melting point is 28000F
- Wrought iron became pasty and very plastic at red heat and could be easily forged at about 16500F
USES:
Since mild steel has replaced the wrought iron, therefore it is no longer produced in large extent. Still in use for roof sheets, wires and metal ornaments etc
STEEL
Steel is an alloy of iron and carbon. Pure iron’s strength remarkably increases when alloyed with carbon. The tensile strength increases with increasing carbon content but the ductility reduces. Steel having its properties because of the presence of carbon alone is called “Plain carbon steel”.
Steel is designated by AISI with four digits, the first two denoting alloying elements and the last two denoting the carbon content.
PLAIN CARBON STEEL can further be classified as
-
Low carbon steel or mild steel:
Low carbon steels contain up to ~0.1% carbon and are not heat treatable. They are used in corrugated sheets, automobiles, and tin cans. It is soft and ductile and is mostly used for construction purpose. Uses of Low Carbon Steel in the construction industry include making Sheets, rods, wires, pipes, hammers, chains, shafts etc.
Mild steels contain 0.15 –0.25 wt% carbon and are also not heat treatable. They have higher strengths than low carbon steels. Mild steel is used in beams, angles, channels, oil pipelines, and boilers. Nb, V, Tican be added to form carbides, which cause precipitation hardening. Cu and P can be added to form weathering steels, which are corrosion resistant. S and Mncan be added to form free cutting steels, which are easier to machine.
-
Medium-Carbon steel :
The carbon content is 0.25 to 0.5 %. The medium carbon steel can be heat treated to achieve high yield strength. It is stronger than the mild steel slightly less ductile. Medium Carbon Steel is used in railway wheels, rails, Shafts and connecting rods etc.
-
High-Carbon steel :
Carbon content is above 0.5%. It is harder and stronger than mild steel and medium carbon steel. High-strength steels have tensile strength over 600 MPa. High-strength low-alloy (HSLA) steel contains small amounts of alloying elements and 0.15 –0.25 % carbon. Ultra-high-strength steels have tensile strength over 1000 MPa. For example: Ni-Cr-Mo low-alloy steel. High Carbon steel is used in keys, knives, drilling machines etc.
Properties of Mild Steel
- Ductile and malleable
- It corrodes quickly
- It can be permanently magnetized
- It is tough and more elastic than cast iron and wrought iron and withstands shocks and impacts well
- It is equally strong in tension, compression and shear
- Its specific gravity is 7.8
- It is not much affected by Saline water
Properties of High-carbon Steel
- Its structure is granular
- It is more tough and elastic than mild steel
- It is easier to harden and then to weld
- It is more difficult to forge and then to weld
- It can be permanently magnetized
- Comparatively it is stronger in compression than in tension or in shear
- It withstands vibration and shocks better
Non-Ferrous Metals and Alloys
Copper:
- A ductile metal with high electrical and thermal conductivity.
- Hardness can be increased by reducing grain size or alloying.
- Brass (copper-zinc), bronze (copper-tin), and cupronickel (copper-nickel) are common alloys.
- Corrosion resistant to due to protective layer of copper oxide on surface.
Aluminum – Lightweight (1/3 the density of steel), reactive, ductile, and malleable.
- Low yield strength can be improved by alloying and heat treating.
- Good electrical and thermal conductor, corrosion resistant.
Magnesium – Low density, good mechanical properties, high thermal conductivity.
- 1/3 the density of aluminum while maintaining comparable strength when alloyed.
- Poor corrosion resistance